It was time to put it all together! (This actually happened in March- these are post hoc posts π )
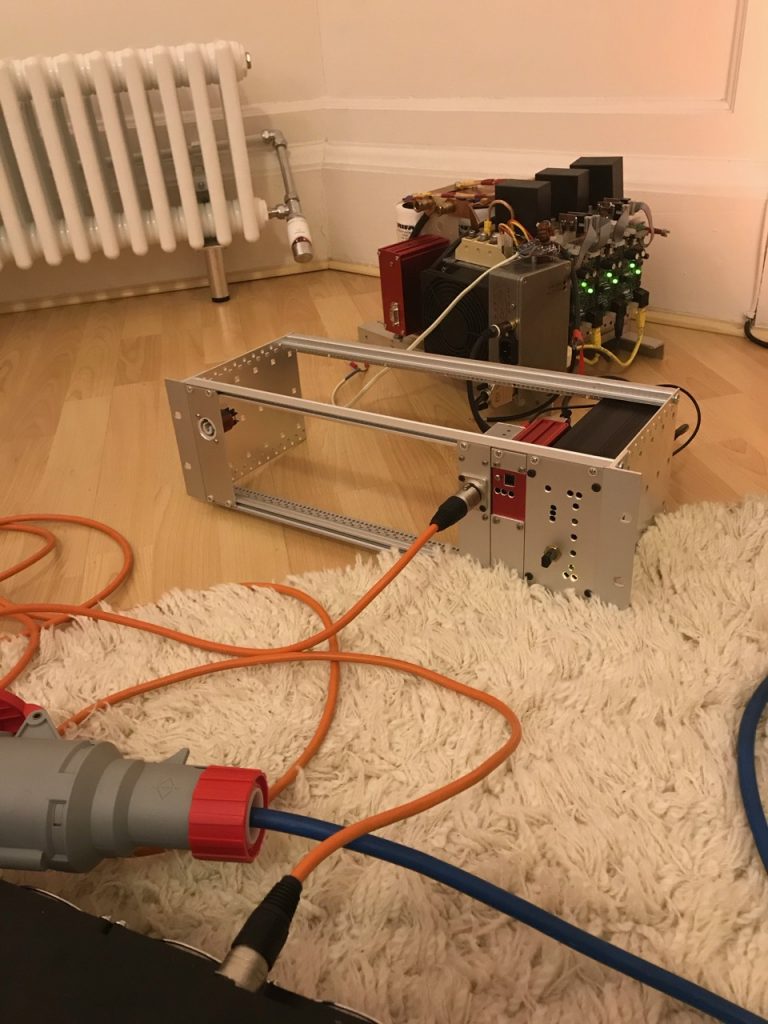
First Odin’s control electronics had to be converted to run off 24V DC instead of the original 240V AC. (And mounted in a Eurorack while I was at it…) This wasn’t too difficult as they already used 20-something volts DC internally, derived from the mains with a traditional iron cored transformer and rectifier, and regulated to 15V.
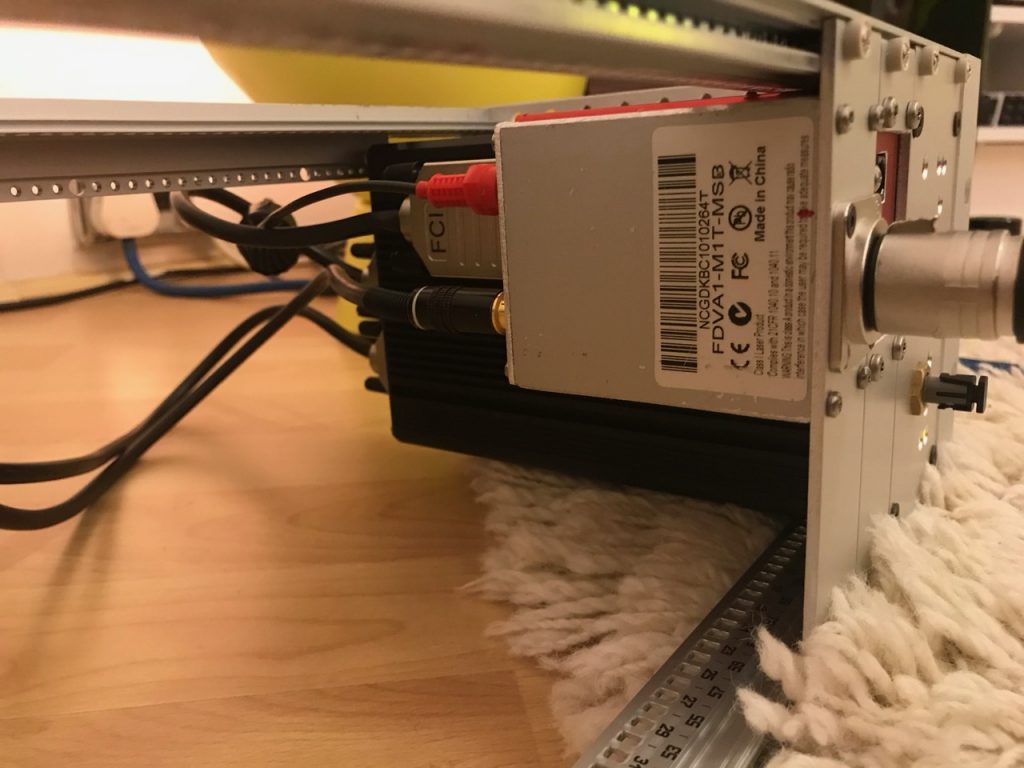
I added DC input sockets to the driver and gate drive amplifier modules, and changed the fan for a 24V one too. The original 240V AC inputs are retained in case the PFC breaks down and I need to change back to the old power supply.
The PFC will be situated at the operator’s position with long cables for 750V and 24V running to the coil. This made everything simpler, as there was no need for remote control and the circuit breaker on the PFC could be the emergency shutoff for the whole system. But it did leave the 24V cable vulnerable to strikes and general pickup of the extreme levels of EMI around a Tesla coil. My solution was to make a DC input module using a surplus Traco 40W DC-DC converter to give galvanic isolation, and lots of EMI filtering on both input and output.
The red module is the receiver for my Teslink system that sends multiplexed control signals over a Toslink optical fibre. I finally got round to completing it (and making a Eurorack mounting transmitter too)
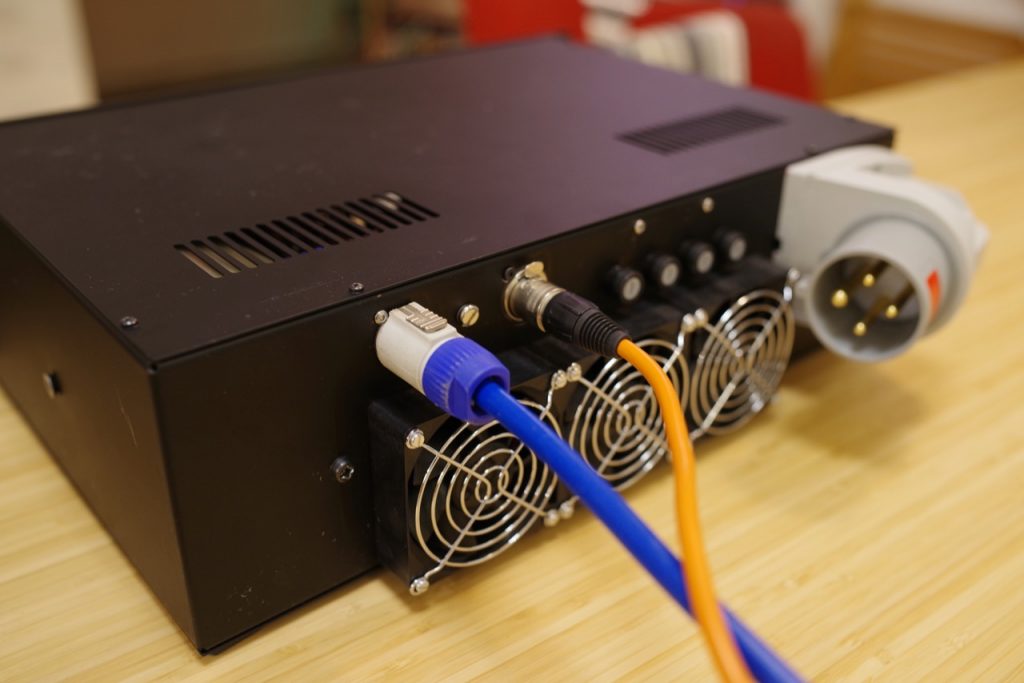
The idea is that the PFC accepts single or 3 phase power at anywhere between 208 and 415V, and supplies 24V DC to the Tesla coil electronics from its own control power supply. I didn’t want the hassle of having to change taps on control power transformers, or rather the carnage of connecting it to 415V with the taps set to 240. (I have done this before- it was messy)
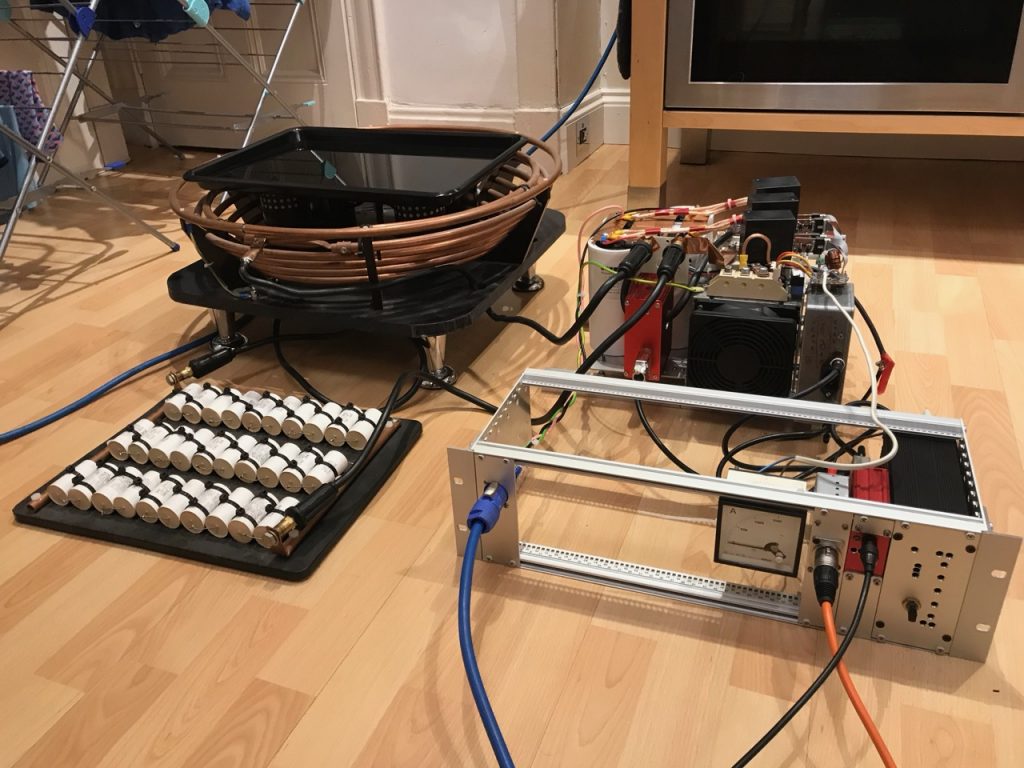
The Tesla coil primary was set up using a water-filled steel pan as a dummy load.
It didn’t explode! π
The next step would have been to take the PFC and immersion heater bucket to a lab with 3 phase 415V power. Unfortunately this was made impossible by the COVID-19 lockdown. The debut was to have been the Nottingham Gaussfest, but this was also cancelled. Insert corona joke here π