Wanted a track light fitting for the living room and more aluminium welding practice π
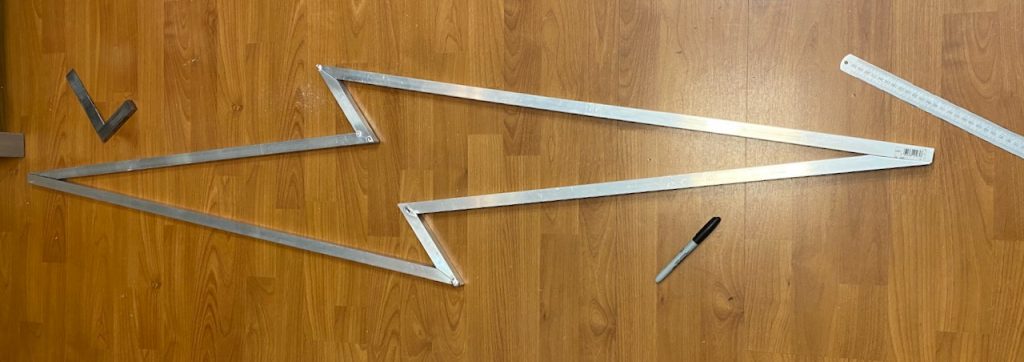
20x20mm square tube (ashamed to admit I bought it from B&Q) was cut into the shape of a lightning bolt.
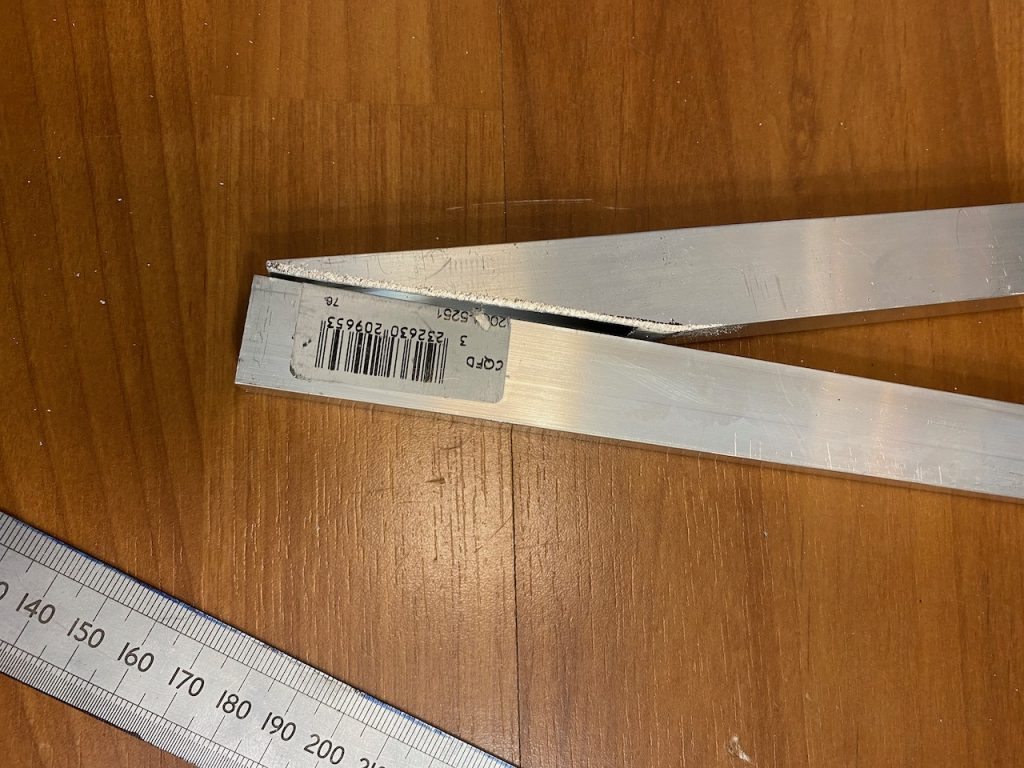
Oh dear, the mitreing could have been better…
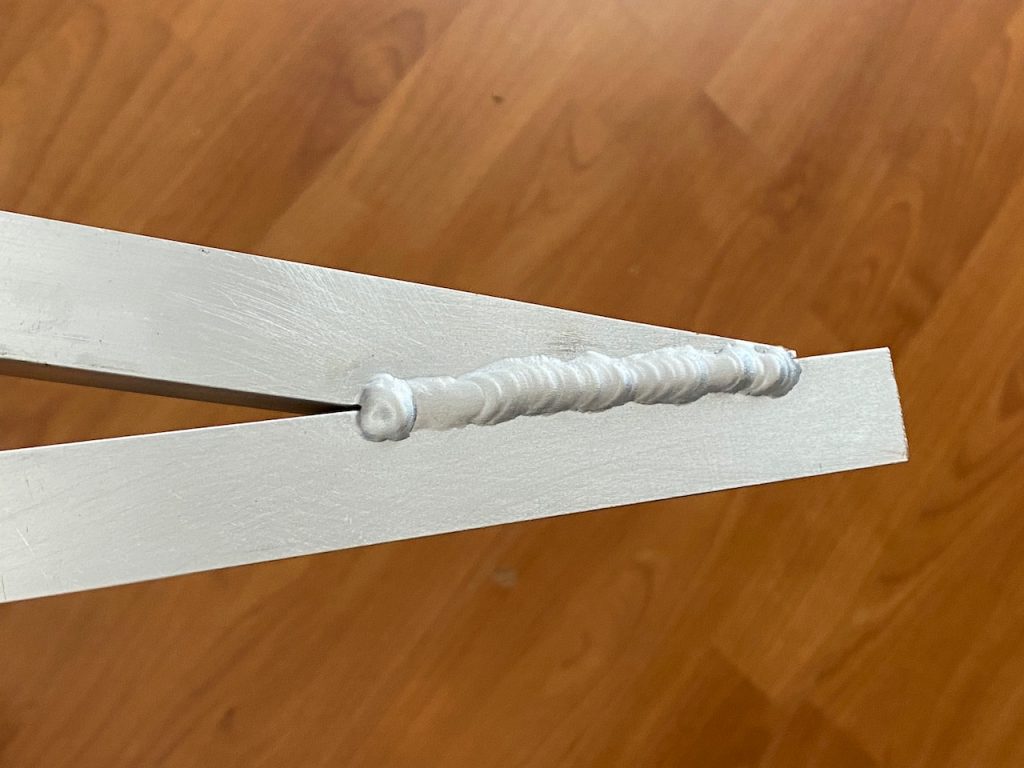
This is the nicest weld, there were much worse π I got off to a bad start by burning several holes in it while trying to tack it together, and had to weld up the holes. I didn’t realise the tubing was only 1.6mm thick and started off with too large a tungsten and too much current. Another reminder to always test the welder settings on a scrap of the material you’re going to use… π
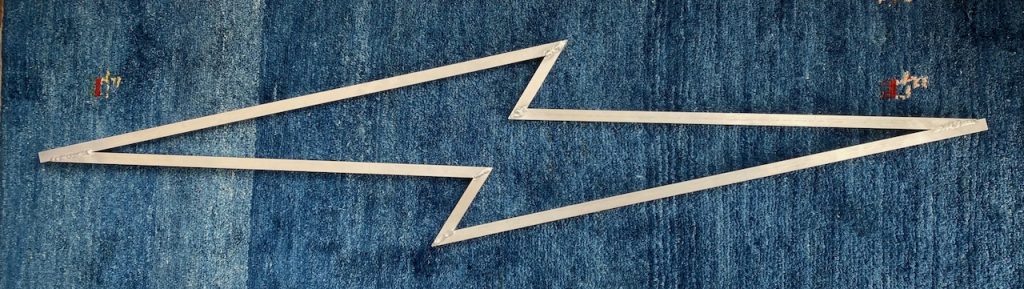
After fully welding (OK I didn’t do the inside corners π )
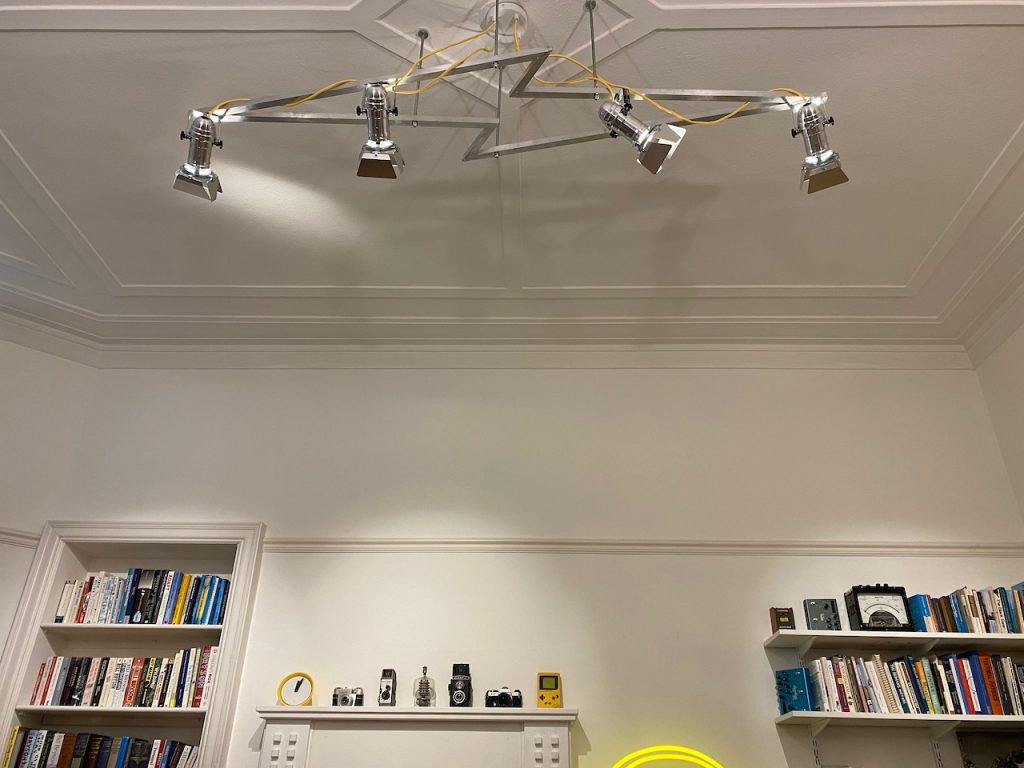
Mount to the ceiling with M8 threaded rod
Mini PAR cans and barn doors from CPC (Should have got the black barn doors!)
Ceiling rose and yellow wire from Creative Cables
Bulbs are 12V LED MR16 from Screwfix connected to the 12V lighting system
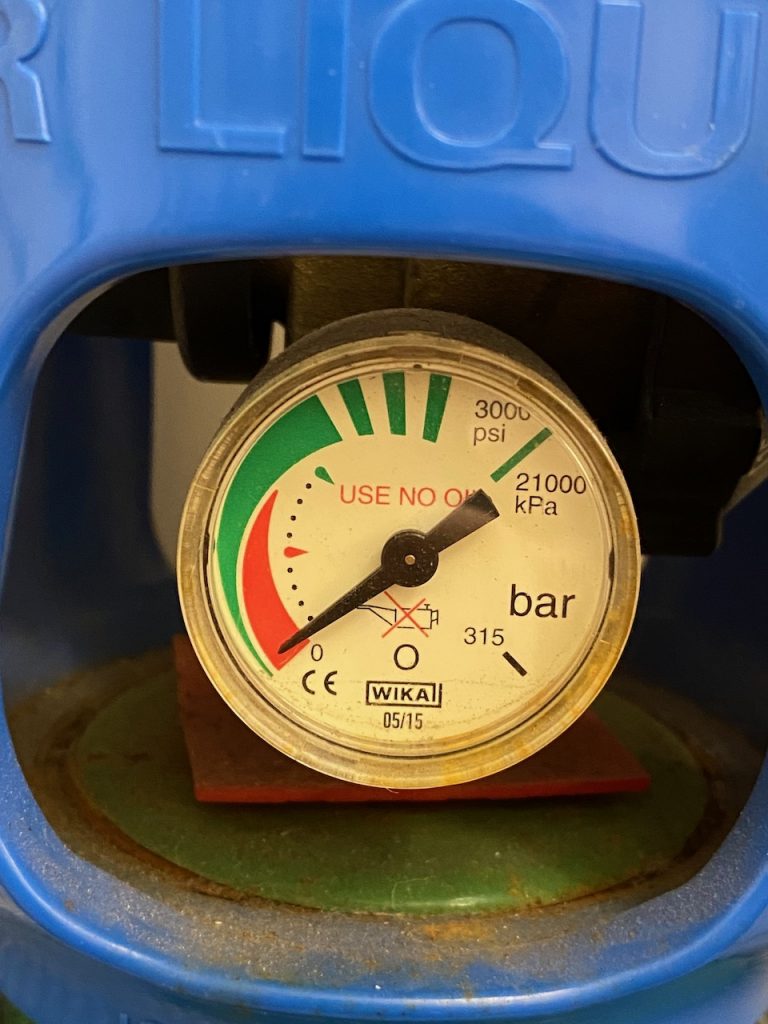
Finally finished the argon tank π