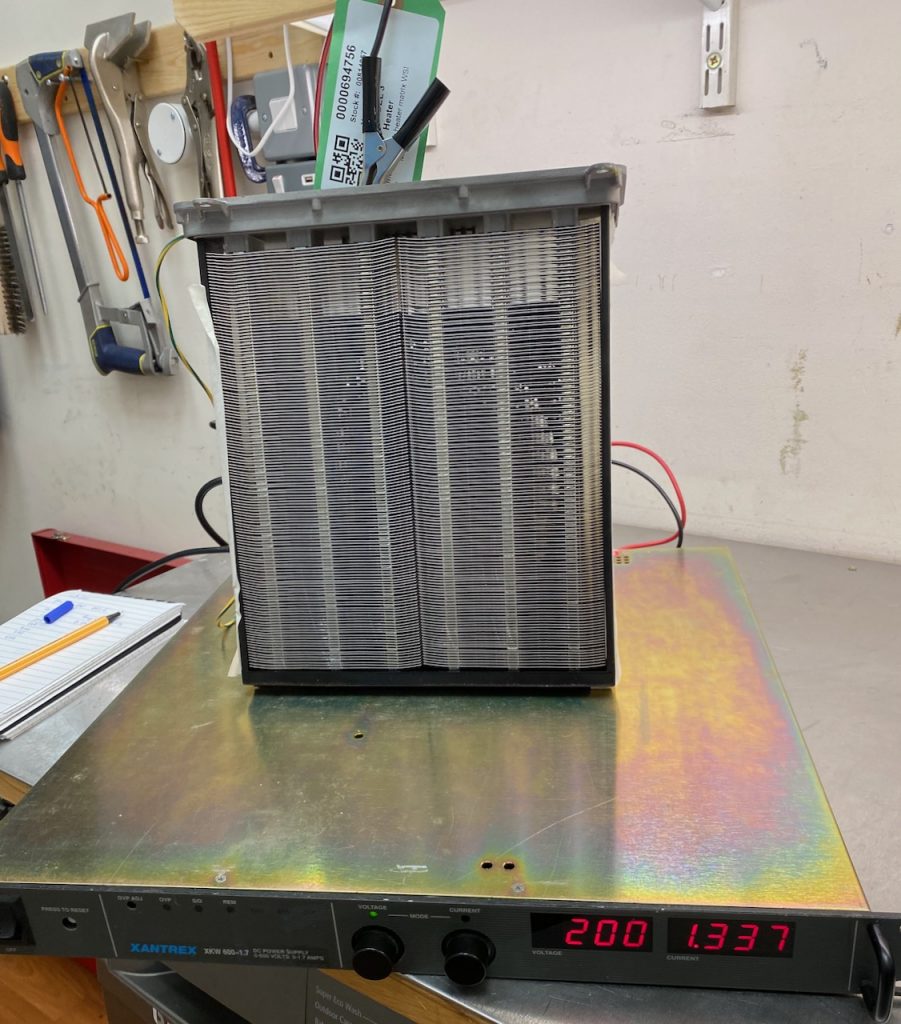
I thought I’d better test the characteristics of the PTC elements in a scientific manner as opposed to just applying 750V DC from the PFC and seeing what happens.
When measured with a multimeter at room temperature, each element read about 600 ohms. This would imply a rather low power output if that was the minimum resistance.
For my next experiment I connected one of the elements to my old Xantrex 600V bench power supply. The 600 ohm cold resistance would imply a draw of no more than 1A at 600V if the element was purely PTC. But to my surprise, the current draw actually began to increase as the element got hotter, eventually hitting the PSU’s 1.7A current limit at only 200V.
This means that the elements must actually start off as NTC, and transition to PTC at a higher temperature. That kind of makes sense, as a car heater matrix has to be able to start up from very low temperatures. Purely PTC elements would presumably exhibit an immense current surge when the heater is turned on after leaving the car parked overnight in Canada. π
I was wondering why Tesla bothered to implement individual control of the 6 elements, and I guess the turn-on surge is the answer to this too: by turning them on sequentially the surge can be made 6x smaller. It’s not like a Tesla traction battery (or even an IGBT) would care if the turn-on surge was 10A or 60, but maybe it allows them to use a lower rated fuse to connect the heater to the battery. Fuses rated for high voltage DC are expensive so the savings made here might outweigh the cost of 5 IGBTs and drivers.
Anyway, I couldn’t test above 200V due to the limited output current. The next larger PSU I have is the PFC, and it has a minimum output voltage of 400V (600 on 3 phase) so I will just have to “send it” as the kids say nowadays.